Vacuum excavators are designed for an extensive range for cleanup and excavation tasks. They use suction or pressurized air to clear tough obstructions and speed up general maintenance. A vacuum excavator also removes unwanted fluids, spills and materials from the source and then displace the waste into a debris tank.
In September 2021, the District purchased a Vermeer CT 573 GT, a low-profile trailer vacuum excavator with a design that keeps the components of the unit accessible. It offers a 30-foot hose with a 3-inch diameter for effective waste removal. The debris tank holds 500 gallons and is lined with polymer to help ease dumping and cleanout. And, the vac’s reverse pressure option helps offload liquids and dislodge obstructions in the hose.
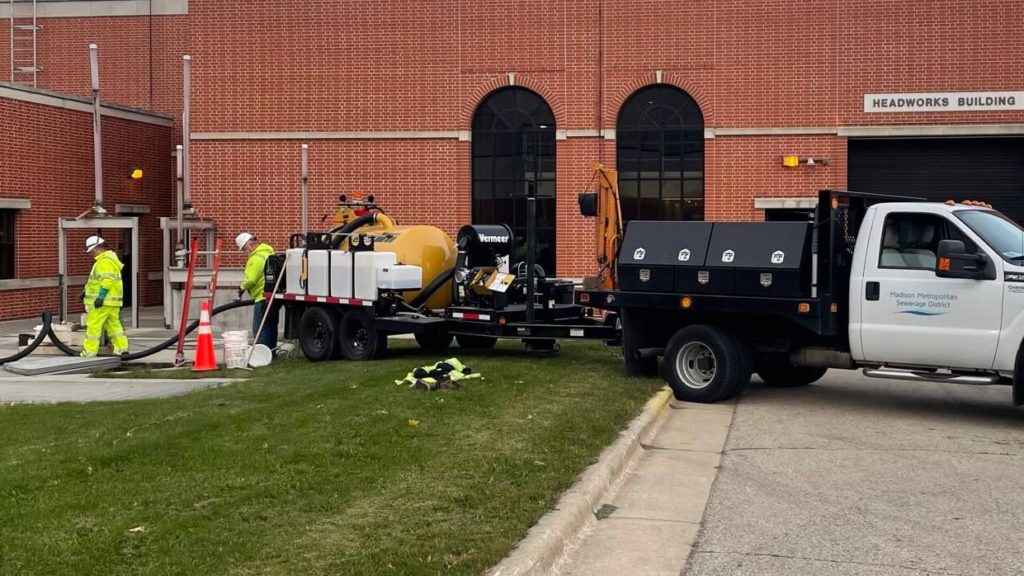
Even though the District just acquired the unit, it’s already been used in many areas of the treatment plant.
“It’s pretty new, but we’ve used it a lot,” says facilities maintenance worker Chris Lothe. “We’ve used it on screens at Headworks and in grit basins and it was awesome. We cleaned primary channels and sucked grease off the top. It’s efficient, works well and you’re not killing your back shoveling.”
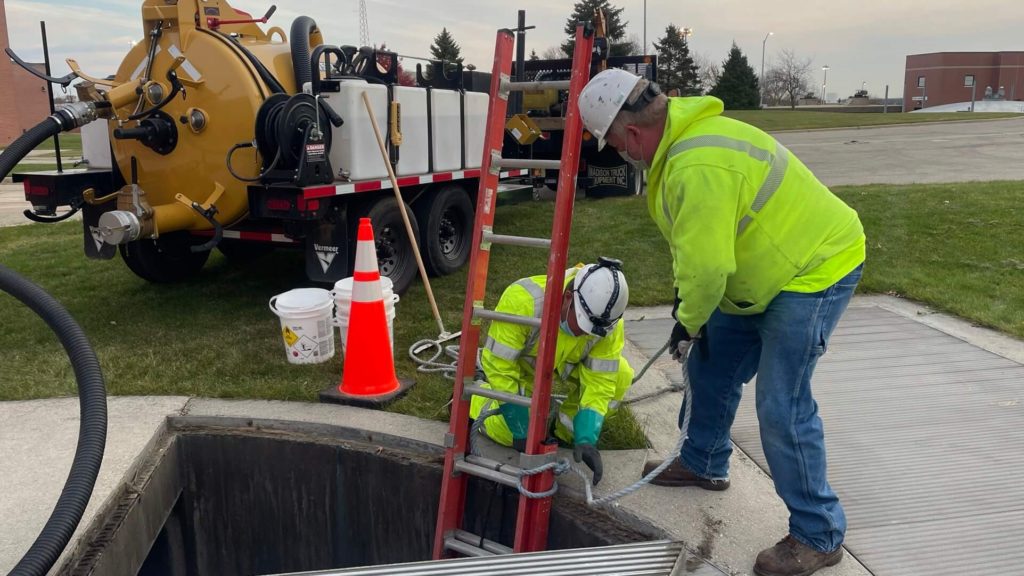
Having the equipment onsite offers additional benefits. Prior to purchasing the vacuum excavator trailer, the District had to hire out extraction services, which required budgeting and scheduling. When the equipment is on site, the time and money saved creates an incentive to use it for both small and large jobs.
“With a vacuum truck company, you have to schedule the service and it costs money,” Chris explains. “This equipment is now in the shop and we can use it whenever, which is a lot more convenient and a lot faster.”
Cleaning with the vacuum excavator
In wastewater treatment, a grit basin or grit chamber is a primary treatment tank designed to slow down the flow of wastewater so that solids such as sand, coffee grounds, eggshells and inorganic material can settle out effectively. Grit is removed early in the treatment process to avoid excessive wear and tear on pumps and other plant equipment down the line.
The Facilities Maintenance team cleaned the District’s three grit basins in October and November 2021. It was the perfect opportunity to test the newly-purchased extraction equipment’s limits against grease, silt, mud and other materials that settled in the grit basins.
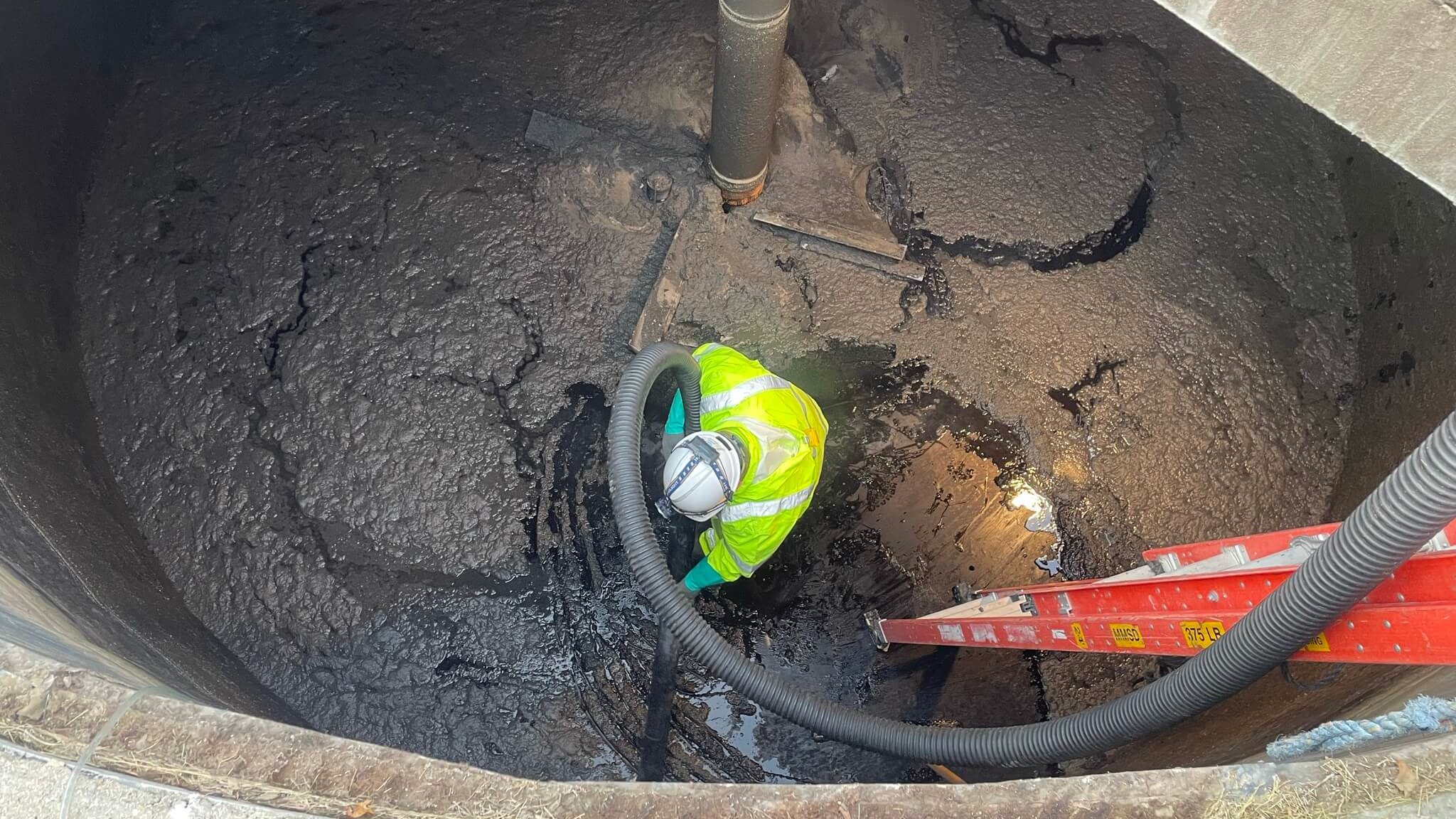
The team observed how the equipment drastically sped up material removal, particularly in high-collection areas like the chamber floors.
“The job went much faster with this equipment,” says Chris. “It would take probably four hours instead of two to clean the basin out if we were to do it all by hand.”
Grit basin discoveries
After the vacuum excavator got rid of the bulk of the material, the team could see that the propellers in the tanks were off kilter and no longer centered. This was caused by the build-up of wipes and other unflushables we call “rags” at the District.
“When there’s too much grit and rags inside of a propeller, it’ll disconnect the blades that turn and circulate the material that’s in the bottom,” says facilities maintenance worker Donnie Martinson. “We clean up the chambers so that the mechanics can get the blades back on and get it working optimally again.”

Unflushables at the plant can create other issues. They can make the primary stage of wastewater treatment less effective, create equipment vulnerabilities that are expensive to maintain and repair, and make a dirtier and more time-consuming job for staff.
“Near the propeller there were balls of rags,” says facilities maintenance worker Ethan Poser, who worked on the grit basin cleaning team. “I used a drag fork and a shovel so I didn’t have to touch as much of it with my hands.”
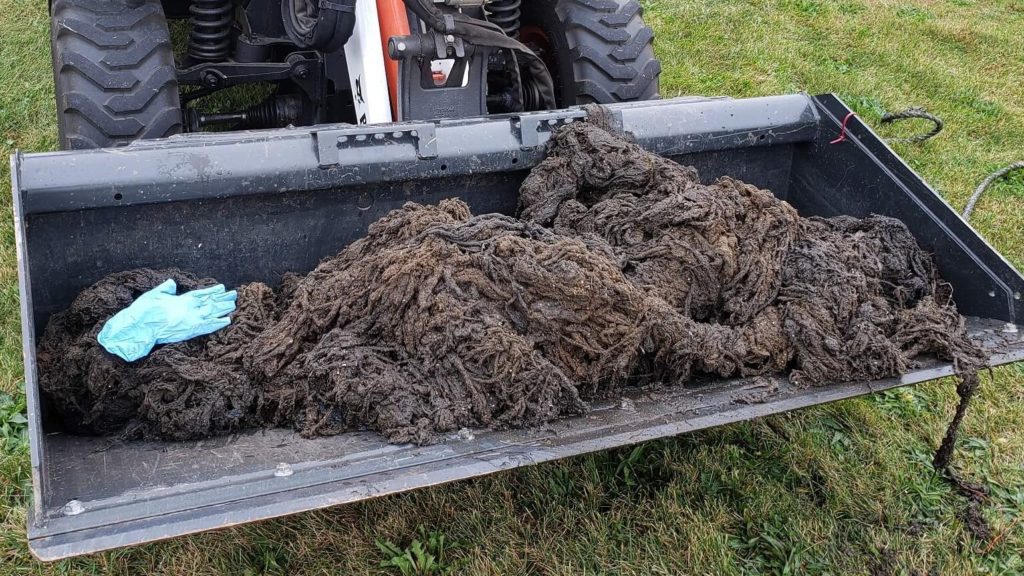
Moving forward, Donnie reflected that the basins should be checked more frequently than they have in the past. “It would help prevent buildup or potential damage to equipment, either in the grit basin or further down the line,” he said.
Erik Rehr, maintenance and reliability manager, agrees.
“Prior to this there was no PM [preventative maintenance activity] set up in the system to inspect and clean the grit basins on a routine basis,” he says. A PM has been set up for six months in the future and based on the findings, adjustments will be made so the units are cleaned at the optimal time.
Different teams, working in concert
When a piece of equipment is slated for cleaning, it’s also a great time for mechanical maintenance without additional disruption to the treatment system. During the grit basin cleanings, mechanics were able to change the oil in the bull gear drives and gearboxes. Perhaps not surprisingly, the jobs took about the same amount of time to complete.
“In colder weather, it takes about 1.5 to 2 hours to change the oil on the grit basin,” said lubrication technician Matthew Rodenkirch. “That’s partly because the oil drains much slower as it cools; it’s a tedious process.”
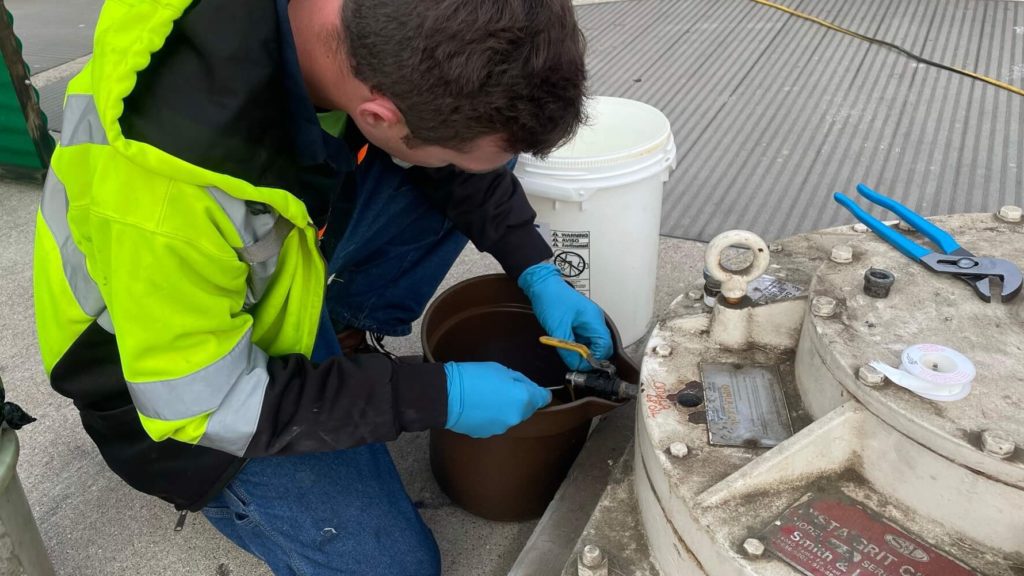
The Mechanical Maintenance team performs year-round service, at regular intervals, on the various equipment around the plant. Greasing sheets are checked and equipment is marked with stickers to help identify timing for equipment maintenance.
“There’s monthly, quarterly, semiannual and annual greasing schedules and in between we do oil changes on equipment all around the plant and at pump stations,” mechanic Dick Hockett says. “There’s plenty to keep us busy.”
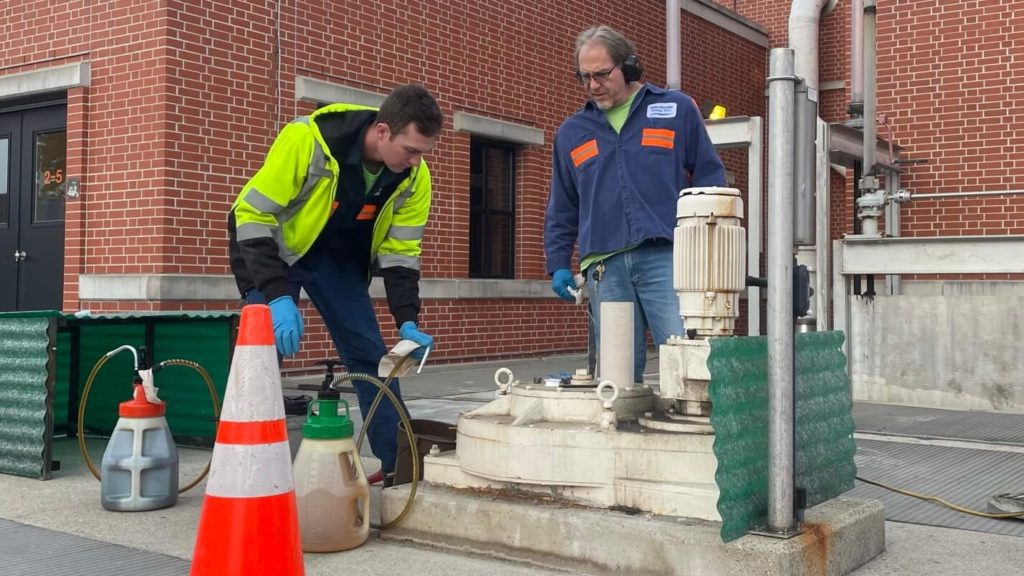
By having the Facilities Maintenance and Mechanical Maintenance teams work hand-in-hand, we reduce downtime of plant equipment, optimize treatment efficiency and help elongate the life of plant equipment. Ultimately, the combined investment by these teams helps ensure lower operating costs and better outcomes for wastewater treatment.
Learn more about operations, maintenance and other wastewater treatment processes on the District blog.
Article written by Amy Steger