In May 2024, the Mechanical Maintenance team completed one of their bigger projects for the year – replacing the shaft and sprocket on the Headworks Screen 4 unit. Replacing the 2,200-pound piece of equipment, as well as other parts in the unit, required a hefty amount of hands-on time by Mechanical and Facilities Maintenance staff, as well as planning and parts investigation by the Reliability Process maintenance planners.
Headworks, where all wastewater from our collection system enters the plant, has three screening units that filter out debris before sending the water through the processing system. Wipes, plastics, and other items larger than 6mm are caught in a rotating screening unit and lifted up and out of the water. Spray nozzles at the top of the unit force the debris out of the screens into a trough. The material is then sent through the macerator well, through a compactor, and is finally deposited in the dumpster.
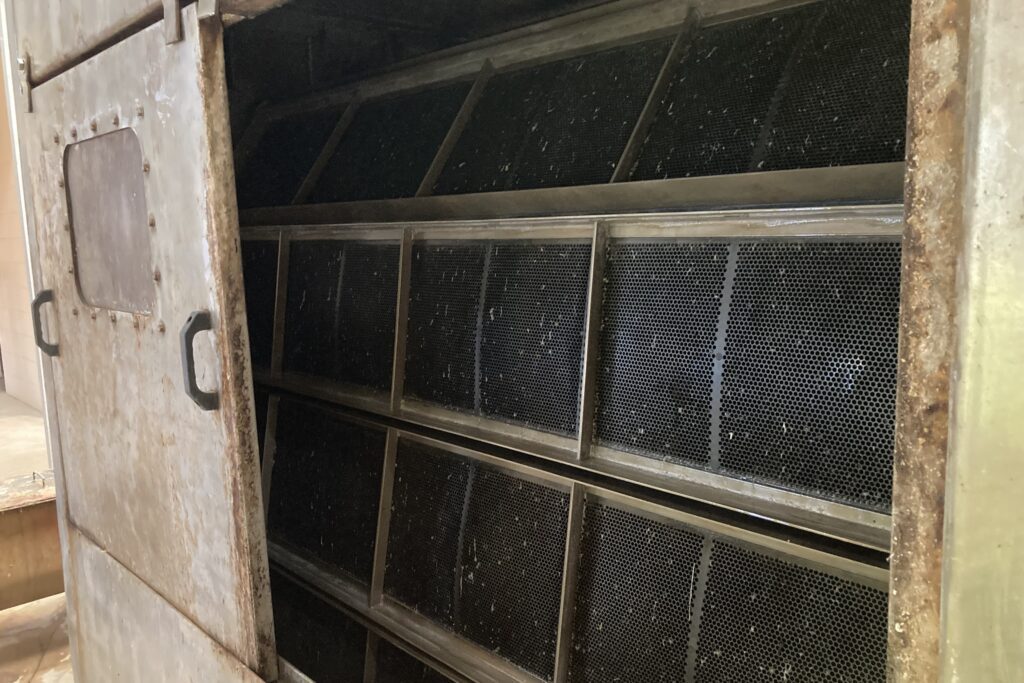
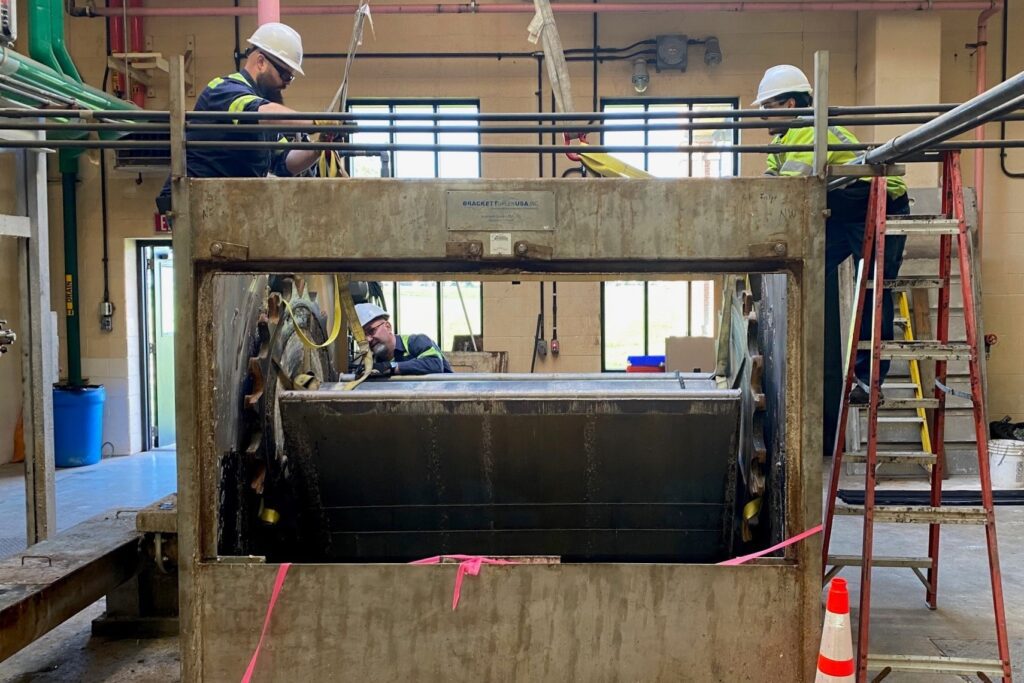
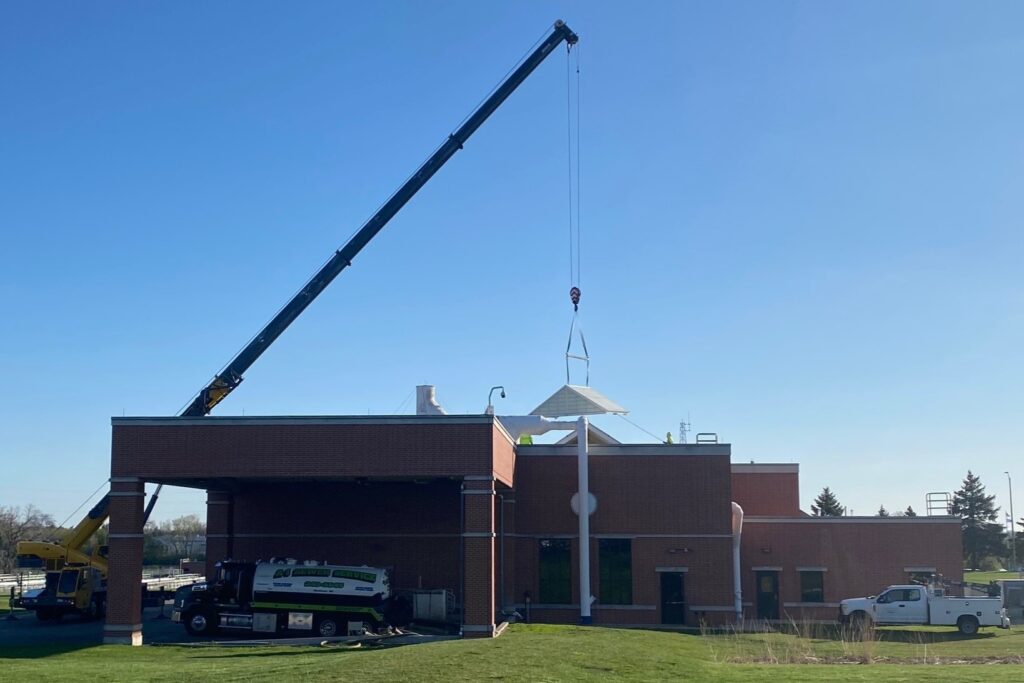
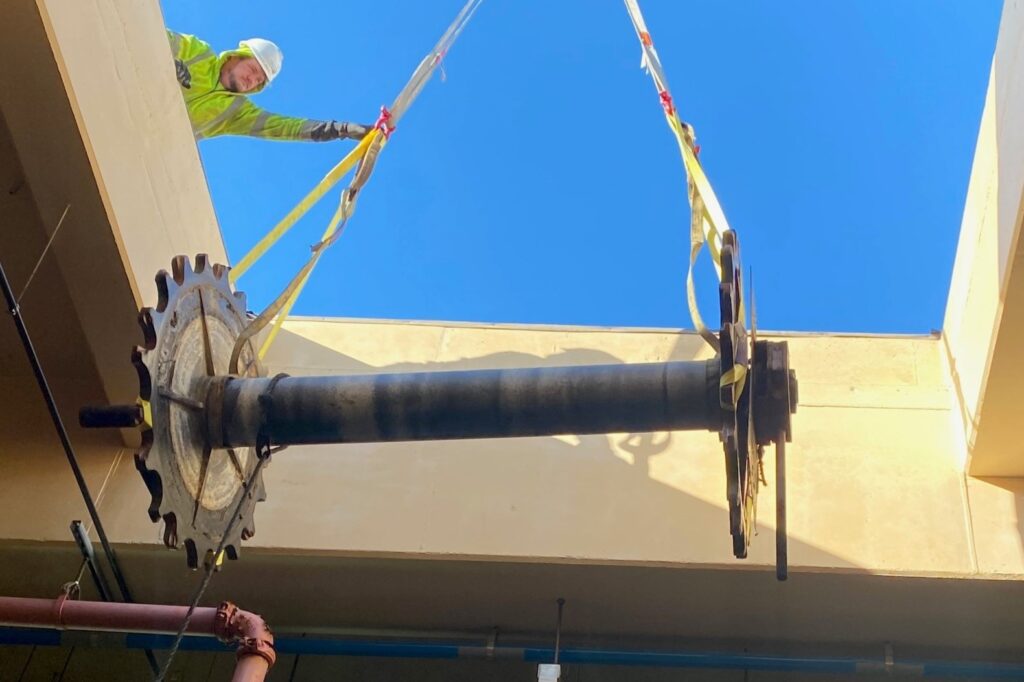
Screen 4 is located closest to the inlet for flow coming from Septage Receiving, so it receives the most debris. This hard-working unit runs almost constantly and requires daily attention from operators who monitor it for clogs.
Mechanics inspect all the screening units weekly and adjust the chain tension on the units monthly. Screen 4 wears out the most frequently of the three units, usually requiring annual replacement of the chain that rotates the screens and the stainless steel strips hat help guide the rollers riding the chain. But, about every 5-7 years, the sprocket and shaft and the bearings in the unit have worn down enough that replacement is required.
Jon Martinson, Mechanical Maintenance supervisor, says replacing the sprocket and shaft involves more complication, planning and time. “Parts first started rolling in about a year ahead of time,” he says of this year’s project, but it took time for them all to come in and for the work to be coordinated and scheduled, including scheduling a crane and crane operator.
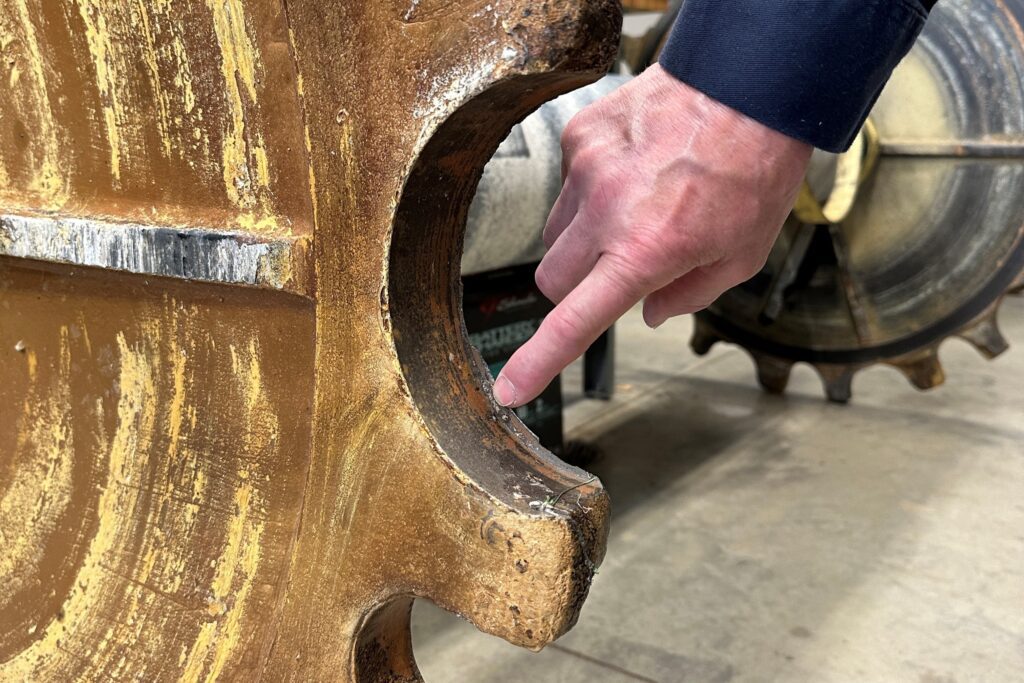
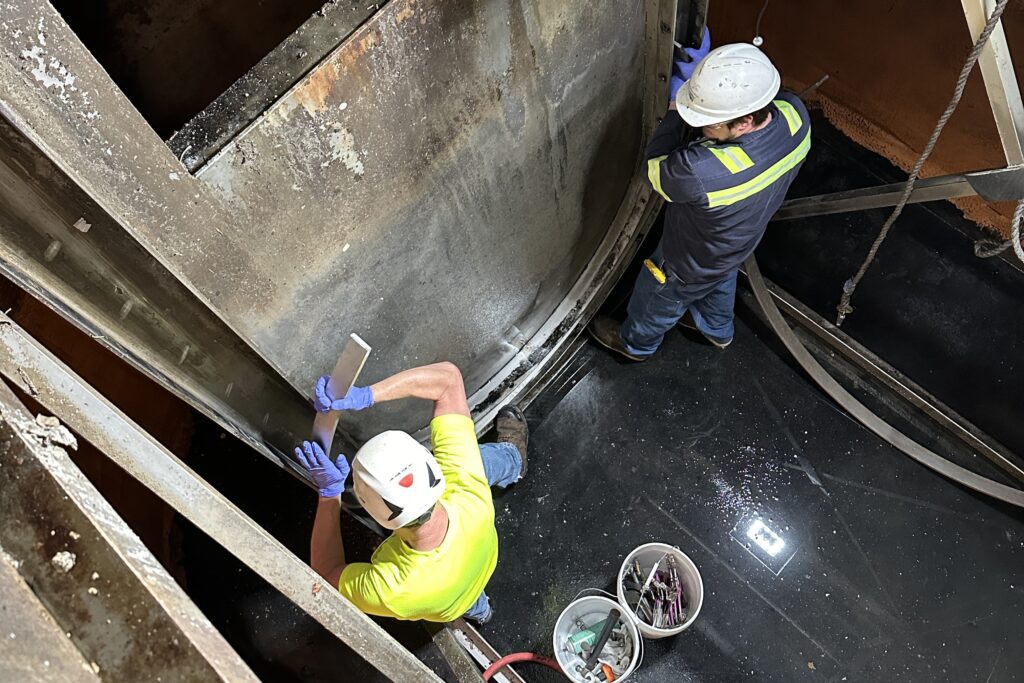
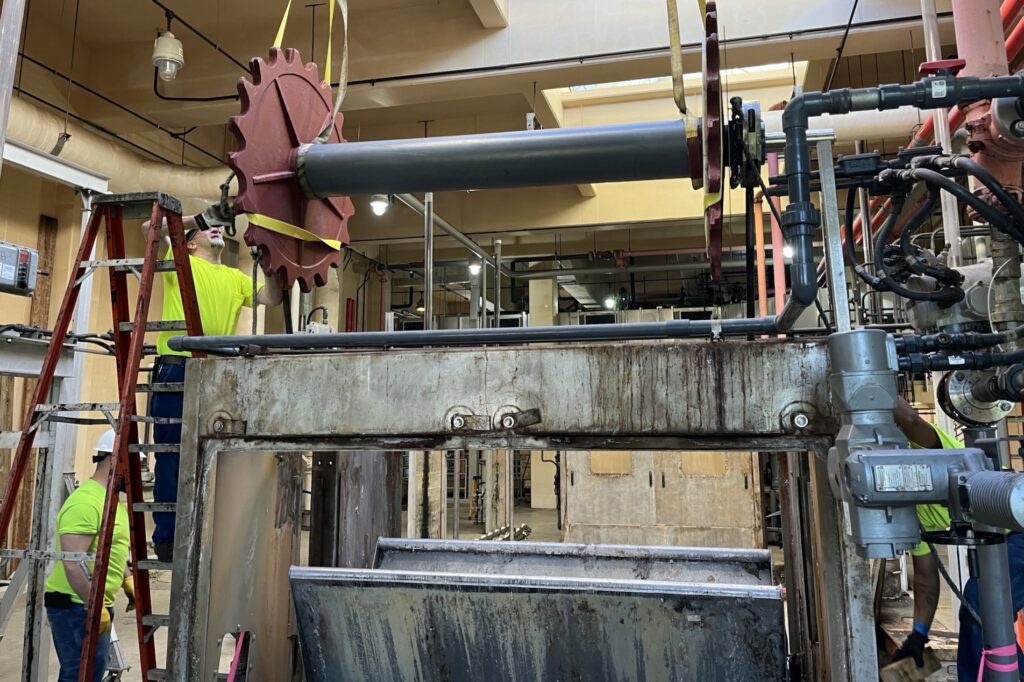
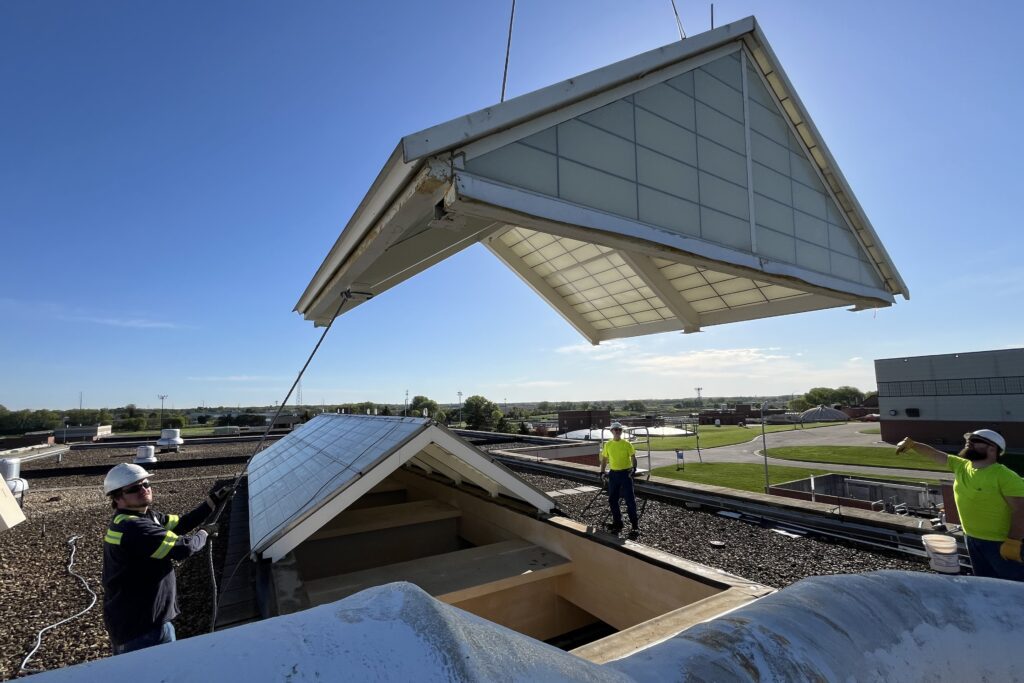
Maintenance planners Logan Miller and Matt Rodenkirch both contributed to the planning and parts procurement for the project. Matt explains that because this project hadn’t happened for seven years, notes about parts and procedures were difficult to find or non-existent, requiring more research and time.
“As maintenance planners, we now have job plans with records for those jobs we know will happen again in the future,” says Matt. “That way someone down the road can look at the job plan tied to the asset and know what parts to order and the procedures for taking the equipment down.”
Jon says everything went well with the replacement, including the extra challenge of utilizing the crane, which requires communication between mechanics on the ground, roof and inside the building as well as with the crane operator. “It’s all blind picking, so we are giving him the instructions on where to go,” says Jon. “Crane operators are talented people.”
Here’s hoping the new sprocket and shaft on Screen 4 give us the far end of that 5-7-year lifespan!
Article written by Jessica Spiegel. Photos by Eric Dundee, Matt Rodenkirch and Amy Steger.