How we protect public health and the environment
Every hour of every day, wastewater from homes, schools, businesses and factories is conveyed to the District’s Nine Springs Wastewater Treatment Plant. Here, we remove contaminants and clean the wastewater before releasing it back into the environment. The entire process takes approximately 29 hours from Headworks to disinfection.
The plant uses a combination of physical and biological processes to clean water; it’s similar to how wetlands, streams and lakes naturally purify water. Biodegradable, organic solids are removed from wastewater, treated and then beneficially reused by farmers as a fertilizer as part of the District’s Metrogro program.
How the process works
Arriving at the plant
Wastewater, which is called influent, travels through our collection system and enters the plant at our Headworks facility. Here, the influent passes through fine screens to remove items that shouldn’t have found their way down the drain or toilet in the first place. This includes items such as wipes, paper towels, feminine hygiene products, dental floss and more.
Wastewater is about 99.9% water; solid human waste is just a tiny portion of wastewater and significantly breaks down as it moves through the collection system. However, other materials, such as sand, gravel and inorganic solids can get into the system. To remove these solids, wastewater passes through grit chambers, which use a vortex action to spin them out to settle in the bottom of the tanks.
Primary settling tanks
From the grit chambers, the influent heads to our massive primary settling tanks. These tanks are about 9 feet deep and between 85 and 100 feet long.
Also called sedimentation tanks, these tanks slow the wastewater, which allows heavier solids to settle to the bottom of the tanks and lighter ones to float to the top. The settled solids are called primary sludge, while the lighter floating solids are called scum and skimmed off. The water leaving these tanks is called primary effluent and contains dissolved organic solids that are easy for microbes to break down during the processes that follow.
Aeration tanks
To begin secondary treatment, the wastewater moves to the aeration tanks where biological treatment takes over. Here, air is pumped into large tanks that mix the wastewater with bacteria and microorganisms that will consume as food the organic matter and nutrients that contaminate the water. The air creates bubbles that help keep the beneficial bacteria and microorganisms moving and hungry.
Final clarifying tanks
Next, the aerated wastewater, along with the bacteria and microorganisms, flow to the final clarifying tanks; this mixture is often referred to as “mixed liquor.” The large, circular tanks, which look like turntables from the air, allow the microorganisms to be separated from the clean water by settling to the bottom of the tanks.
Most of these microorganisms are recycled back to the aeration tanks to clean more water; the rest are continuously cycled out of this process to make way for new, hungry microorganisms. The retired microorganisms aren’t wasted though. In the process of cleaning the water, they take nutrients such as phosphorus out of the water. These nutrients are problematic if they stay in the water, but on land, they help things grow and are made into the District’s biosolids fertilizer product, Metrogro, via the biosolids handling process
Once the water leaves the final clarifiers, it has completed secondary treatment, and is now called effluent, which is cleaned wastewater.
UV disinfection
Because our effluent is returned to surface waters where people could come into contact with the water through fishing or boating, in the higher recreational-use months of spring, summer and fall, the water undergoes an additional process: ultraviolet (UV) disinfection. Here, the effluent passes through high-strength UV lights designed to deactivate disease-causing bacteria before the water is returned to the environment.
The District made the switch from chlorine to UV disinfection in 1986. At the time the first system was built, it was the largest UV system in the world.
In 2021, the District brought a new UV system online. The new system saves money and energy thanks to fewer bulbs that are more efficient, which means less maintenance. The new system is also more effective at disinfecting wastewater thanks to new technology.
Back to the environment
After secondary treatment (and disinfection depending on the time of year), the effluent is returned to the environment. The majority of the District’s effluent is returned to Badfish Creek, which is part of the Yahara River watershed; this watershed covers most of the District’s service area. A small portion of effluent is returned to Badger Mill Creek, which is part of the Sugar River watershed. The City of Verona lies in this watershed.
Biosolids handling process
During wastewater treatment, biodegradable, organic solids are separated from liquid waste in the primary clarification step. This solids stream is termed “primary sludge” and is generally very rich in energy potential. Additional solids are created in the activated sludge process from the reproduction of the billions of microorganisms that treat wastewater. This sludge stream is referred to as waste activated sludge, or WAS. Once treated, these solids can be turned into a biosolids product called Metrogro, which is a valuable resource for local farmers and landowners.
To create our Metrogro product, the solids move through their own treatment process. After being siphoned out during various steps in the liquid treatment process, the solids are passed over a series of belts and through filters to reduce excess liquid for more efficient treatment. The solids are then subjected to high temperatures in an anaerobic digester to break down and stabilize the solids. This process also creates biogas, a reusable resource we use on site to produce power and heat for the process and offset our energy demands. This anaerobic digestion step stabilizes the solids and reduces bacteria and pathogens. The resulting product is referred to as biosolids and is thickened a final time before storing and subsequent transport to local fields for application.
Before the Metrogro biosolids product is applied to local fields, it is thoroughly tested. In addition, fields intended to receive Metrogro are carefully vetted following protocols established by the Wisconsin Department of Natural Resources to ensure the health of local residents and waterways.
See this process in action!
Helpful Resources
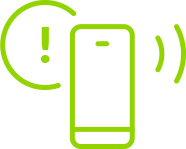
Phone Numbers
Important phone numbers, hours, maps and more
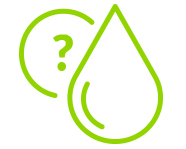
District FAQs
Find frequently asked questions and resources here
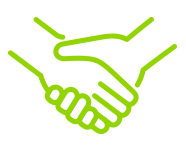
Commission
Find meeting materials and meet our Commissioners