Would you want to predict the future? At the District, we answer with an ABSOLUTELY when it comes to equipment malfunction or failure. Predictive maintenance strategies are our go-to crystal ball.
Predictive maintenance (PdM) techniques help us determine the condition of our equipment so that we can identify when corrective maintenance should be performed. Examples of PdM can include vibration monitoring, thermal imaging, ultrasonic analysis and oil analysis. By using data-driven, proactive methods, we can preplan and schedule maintenance at the most convenient and cost-effective time and maximize equipment lifespan.
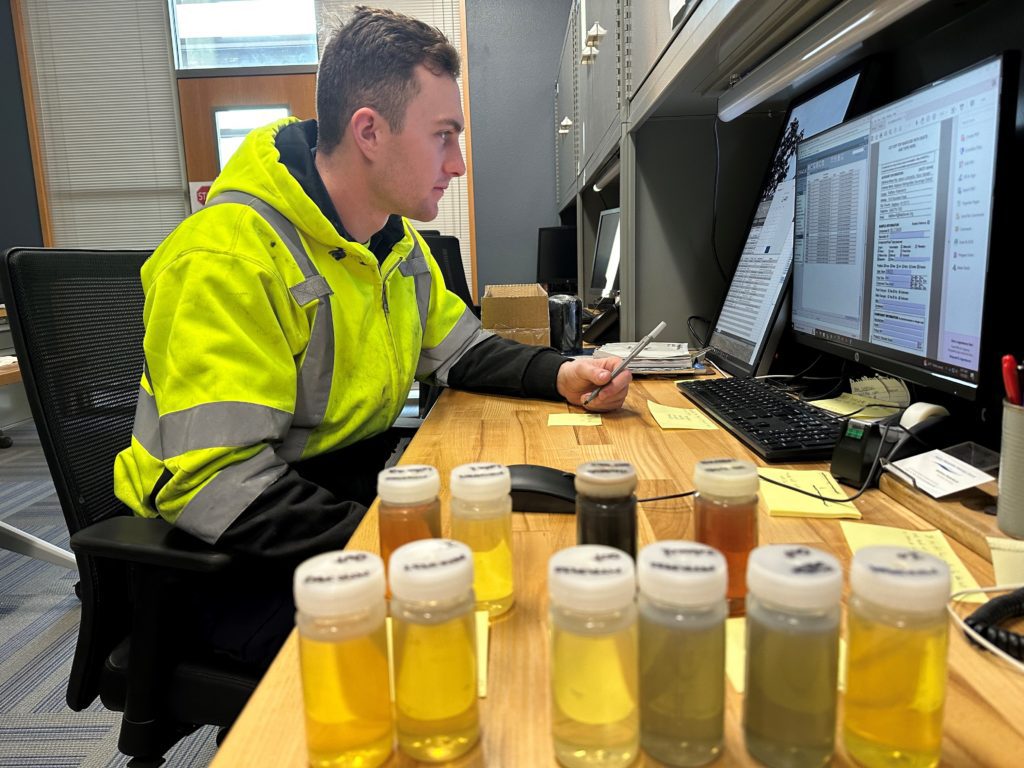
Oil as an early warning system
Sampling and analyzing oil can help teams monitor equipment performance and utilize insights to make better decisions. It’s one of the most effective ways to maximize the protection of our equipment and prolong the life of lubricants.
“Taking oil samples and conducting analysis allows us to get an inside look at what’s happening in the equipment,” says lubrication technician Matt Rodenkirch.
We use oil sampling as a form of PdM to catch the initial stages of machine failure before an issue occurs. It’s an early warning system of sorts that helps reduce downtime and improve overall plant performance.
Examining the oil samples
During oil sampling, we take small samples of oil, typically from larger equipment or assets that are critical to plant processes. Once the oil is returned, we look at three specific measures: acid number, particle counts and metal contents.
The acid number (AN) helps estimate the amount of additive depletion, acidic contamination and oxidation. “We can think of the acid number as the lifetime of the oil,” says Matt. “The acid number measures how much the oil has broken down, and essentially how much more additives are remaining.” The higher the AN, the older and more used the oil is.
Particle counts help determine whether the oil is clean enough for reliable operation. Some consider it to be the most critical test in oil analysis. As the oil runs, it gets thicker and more particles accumulate. Particle counting helps us look at how much debris and critical clearance particles are in the oil. If clearance-sized particles are present, they can result in slow response or surface erosion or can cause safety systems to fail.
“Particle counts are measured in microns, with results typically indicating how many particles of a certain size exist in a sample,” Matt notes. “The higher the particle count, the dirtier and more contaminated the oil is.”
Finally, we look at the metal contents of the oil. For example, if nickel and copper are present, they can act as early detection for potential bearing failures. When other metals are present, they can identify a larger, more underlying issue with the equipment.
Observations from lubricant analysis
Sampling and analyzing oil allows us to plan and predict what may be wrong with a piece of equipment, as well as other attributes like costs associated with oil changes and labor. Conducting oil analysis provides us with five key observations and takeaways:
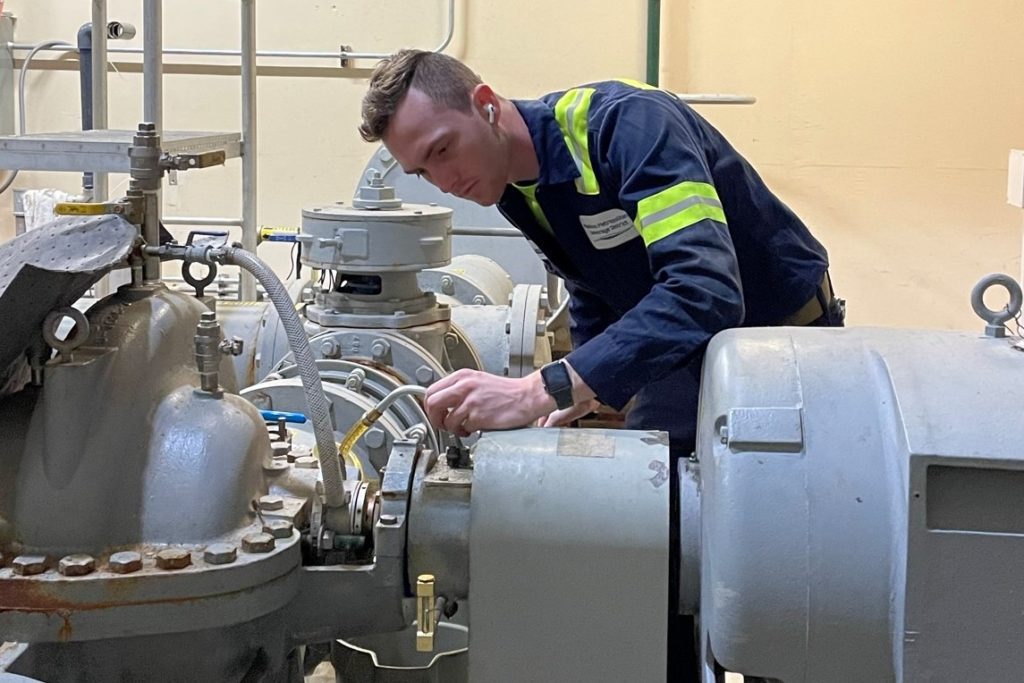
- Lubricant Compatibility
Taking initial oil samples on new drums when they are delivered helps us verify that the oil is the correct viscosity before it is filtered and used in equipment. - Initial Lubricant Cleanliness
Samples taken after we filter the new oil provide the baseline particle count and reference measurements. These show how well our oil filtration equipment is working. - Machine Lubricant Health
We can identify the remaining life of the oil in the machine based on acid number, viscosity and original additive content. - Intermittent Lubricant Cleanliness
At this stage, we can track the particle count in used machine oil (vs. new oil) over a designated run time. We also look deeper at critical clearance particle counts that can damage machine components. - Machine Health
Based on metals analysis, we can determine the condition of gears, bearings, etc.
While there is some overlap between the two oil cleanliness observations, they are separated in this list because we measure cleanliness at two different stages for different reasons.
Oil analysis spells success for RCM
Oil analysis has become a successful part of our Reliability Centered Maintenance (RCM) program at the District. So successful, in fact, that we’re looking to expand the oil sampling program.
“In 2023, the Maintenance Department is looking at expanding the predictive maintenance aspect of our RCM program,” says Erik Rehr, maintenance and reliability manager. “We hope to add additional assets to the oil analysis program, as well as incorporate ultrasonic bearing monitoring as another predictive technology.”
To learn more about our RCM program, check out the article “Reliability Centered Maintenance: Forging a future in RCM” on our blog. Special thanks to Matt Rodenkirch, Erik Rehr and Amy Steger for their contributions to this article.