Part of the biological nutrient removal process used at the plant involves WAS, or waste activated sludge. Microorganisms in the treatment process do the good work of consuming the organic matter and nutrients we want removed from the wastewater – particularly phosphorus. Eventually, there is a surplus of these microbes and some need to be pulled off of the playing field. These
become WAS. They are pumped to the WAS blend tanks where they are held and allowed to release their accumulated phosphorus. This phosphorus is then captured and turned into fertilizer through the struvite harvesting process.
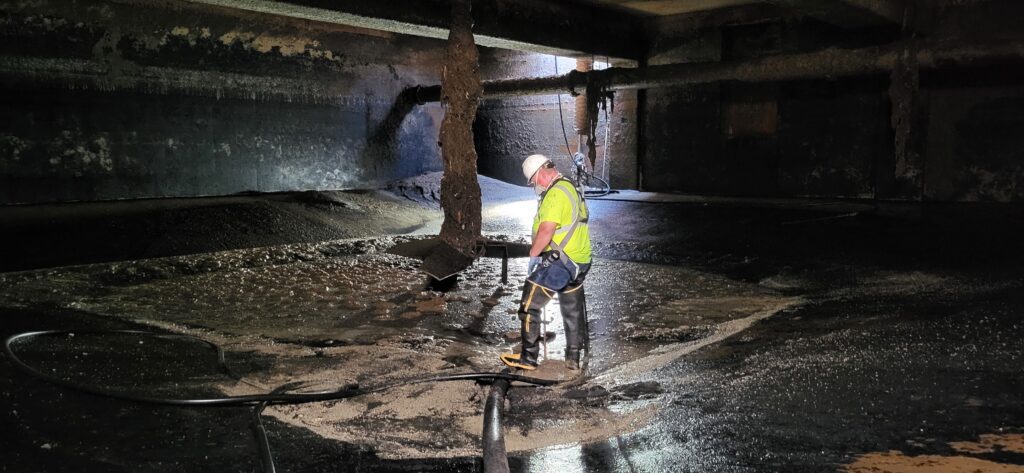
The infrastructure for recovering phosphorus in the form of struvite was put in place in 2014, as part of the Eleventh Addition to the plant. With the tanks getting close to ten years in use, the
Operations team decided it was time for an inspection.
Optimal efficiency check
Matt Seib, process and research engineer, says the main driver for the inspection was to make sure the struvite harvesting process is running optimally. “We wanted to know if debris accumulating in the tanks was preventing us from being as efficient as possible – could we increase the amount of phosphorus recovered?” says Matt. “It also was an opportunity to inspect the equipment.”
The results? “Better than anticipated,” says Matt. Though there was rag debris and some grit, it was not enough to negatively impact phosphorus recovery. Maintenance and reliability manager Erik Rehr was also pleased with the inspection of the concrete walls, mixers, instrumentation and a special floor coating installed to protect the floor from mixer abrasion.
“There was not much surface degradation of the concrete from hydrogen sulfide, and the coating on the floor of the tank was intact,” says Erik.
Pleased with the positive findings, Matt expects the tank won’t need inspection for another eight to ten years.
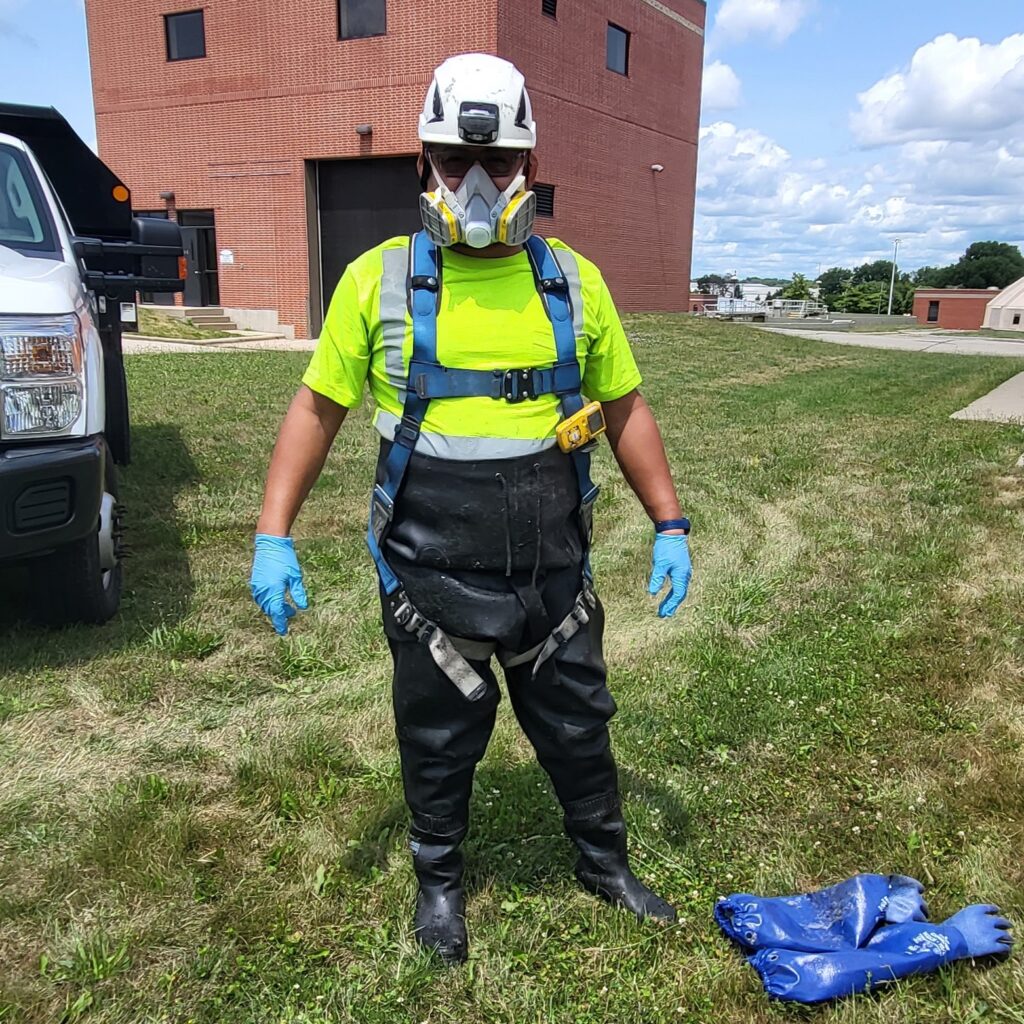
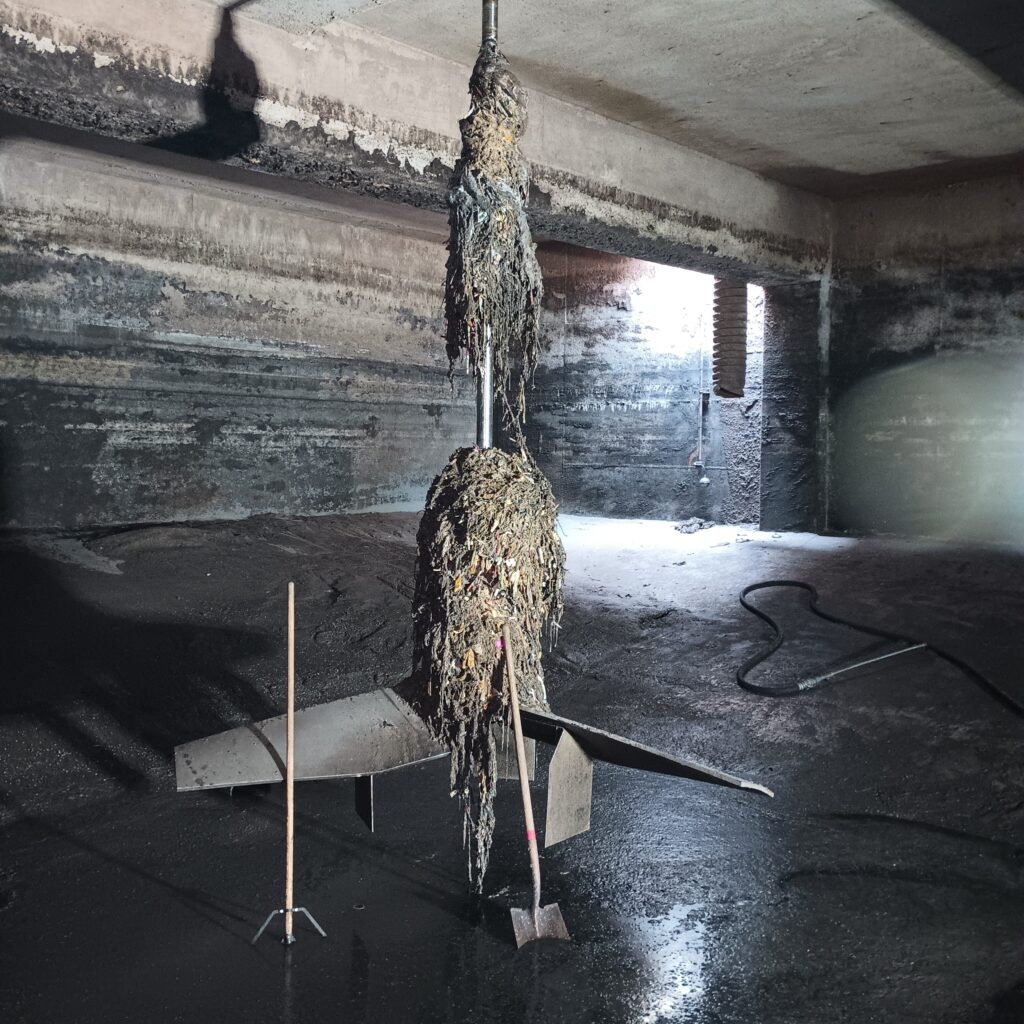
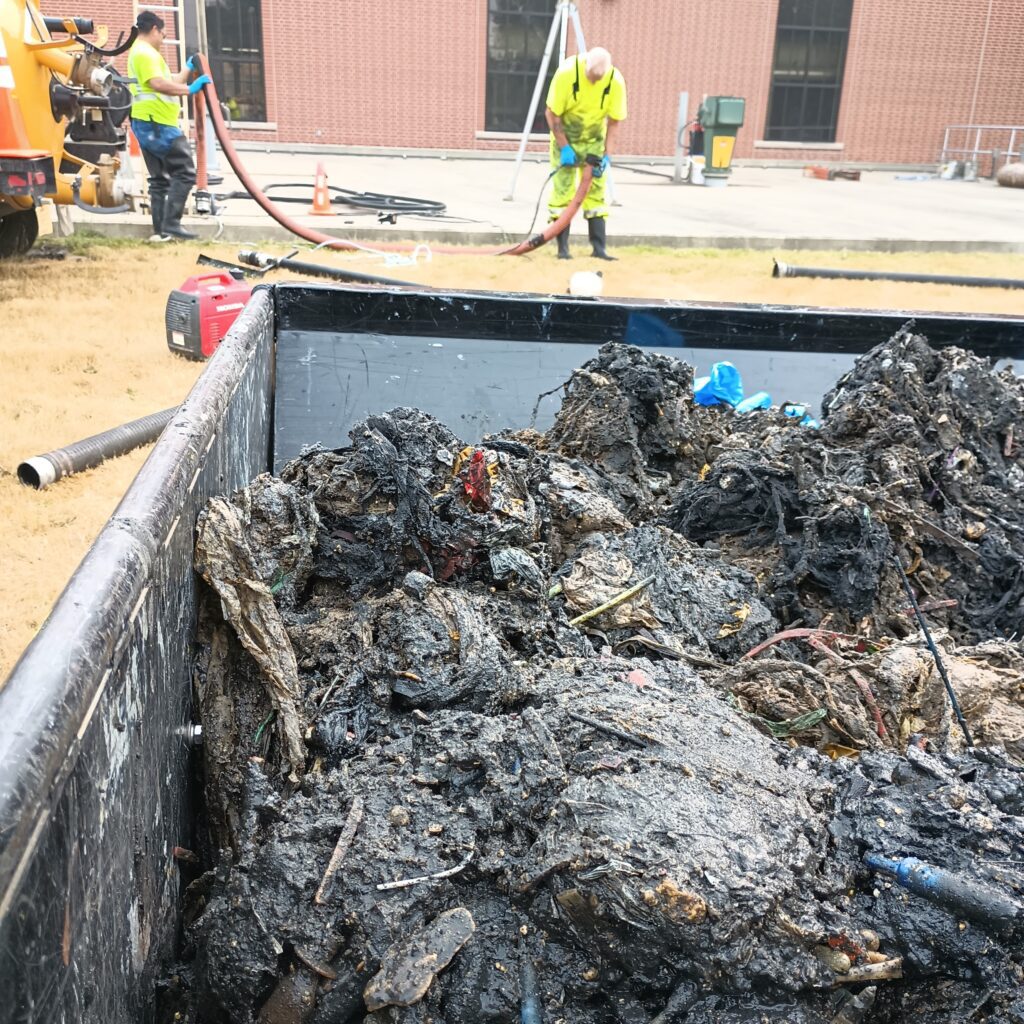
In the tank
The Facilities Maintenance (FM) crew performed the hard work of executing this project — and this was no small job. Tank 1 took over 40 hours of labor and tank 2 almost 60 hours.
After operations staff pumped down the tanks as best they could, the FM crew pumped out any remaining sludge with a Boeger pump, washed down the tank and then dewatered it using the vac trailer. Two or three crew members entered the tank and removed the rags caught on the mixers with drag forks. The rags (and unfortunately, a lot of needles in the rags) were stuffed in 5-gallon buckets and hauled out of the tank – 30 buckets from tank 1 and over 40 buckets from tank 2. Kudos to the FM team for their excellent work!
You can visit our blog for additional project spotlights and interesting articles about the District.
Written by Jessica Spiegel. Photos by Brenda Staudenmaier.